In 2018, our company successfully signed a three-year top drive maintenance contract with Zhonghaiyou Zhanjiang Company to continue the maintenance of Zhonghaiyou Zhanjiang VARCO TDS-9SA TDS-10SA TDS-11SA top drive.
Maintenance plans are implemented according to the standards of NOV manufacturers.
Workshop disassembly and maintenance content:
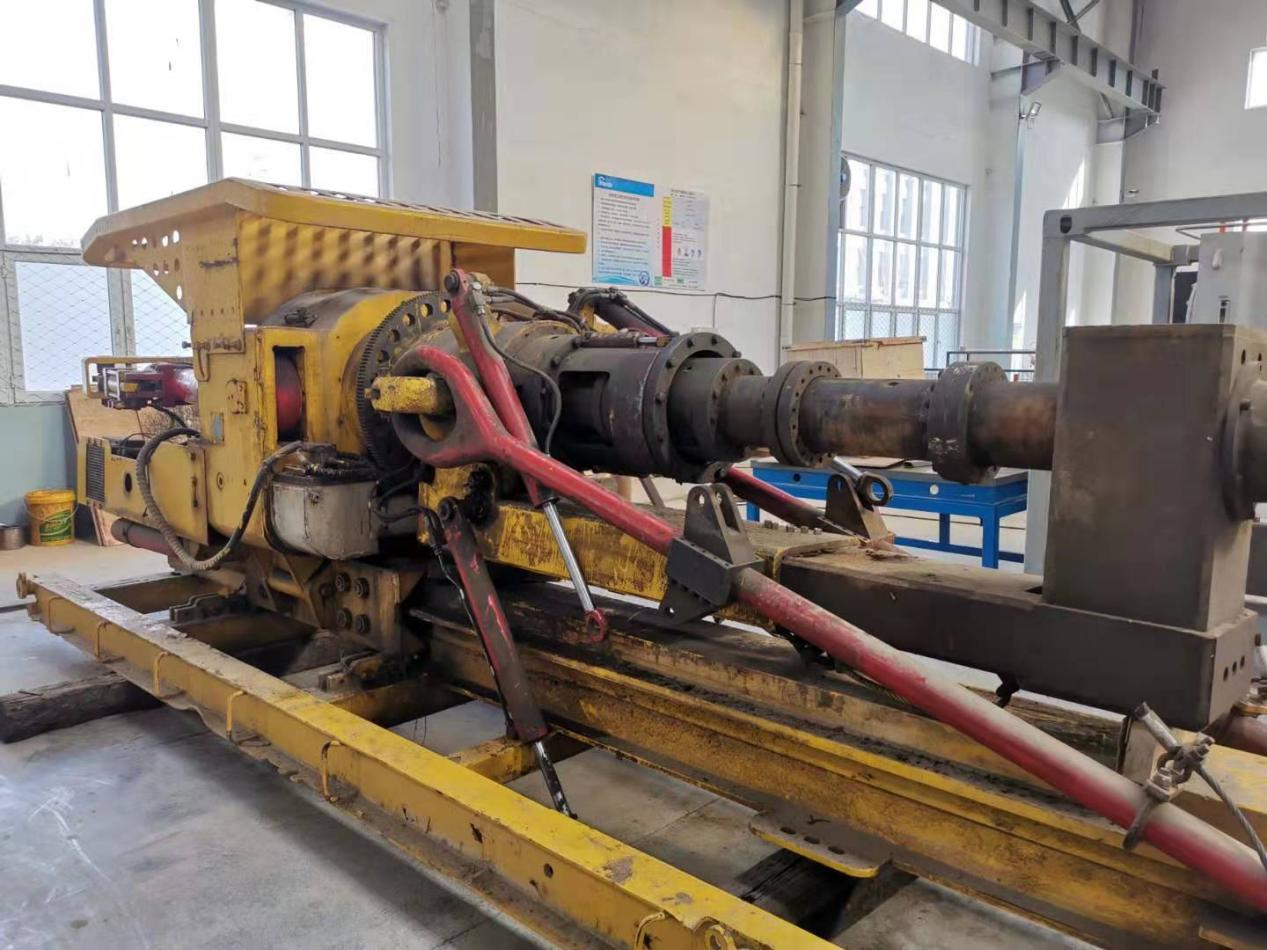
1. Remove the top drive cover
1. Remove all non-equipment spare parts, wire ropes and other sundries on the equipment, drain the oil in the equipment, and thoroughly clean the top drive and track assembly.
2. Disassemble the upper and lower BOP assemblies on the well site and loosen them.
3. Mark the removal of electrical parts (cables, sensors, magnetic valve, pressure switches, etc.) and hydraulic parts (hydraulic cylinders, hoses, valve blocks, etc.).
4. Remove the PH55 pipe processor assembly and rotary head assembly.
5. Dismantle the fan assembly, brake assembly, hydraulic motor assembly, main motor assembly, oil tank and lifting ring, and completely remove the shell of the motor.
6. Completely remove the rotary head assembly.
7. Completely remove the PH55 pipe processor assembly.
8. Completely dismantle the main valve block and take out all valves, pipe fittings, plugs, etc.
9. Completely remove all hydraulic cylinders, accumulators and oil tanks.
2. Inspection and painting
1. Carry out ultrasonic and magnetic particle flaw detection on the center pipe, bail and bail pin, and issue a flaw detection report.
2. Carry out magnetic particle inspection on the rotating head shell, gear box shell, bearing shoulder and suspension ring, and issue an inspection report.
3. TDS-10SA top drive body
1.2.3.3.1. Faucet/drilling motor assembly
1. gear box
A) Clean the gear box, dredge the oil passage, and replace the damaged oil nozzle.
B) Replace all bearings of gearbox (upper centralizing bearing, lower centralizing bearing, transmission gear bearing and main bearing).
C) Replace all the seals of the gear box.
D) Check the meshing clearance of gears at all levels in the gearbox, the wear of gears, and whether there is any trace of corrosion or rust on the tooth surface, and continue to use or replace them according to technical standards.
E) ultrasonic and magnetic particle inspection shall be carried out on the gearbox shell, and the inspection report shall be issued.
F) Assemble the gear box assembly according to NOV standard.
2. Spindle
A) Check the linear runout, radial runout and axial runout of the spindle.
B) Check the spindle bearing shoulder, upper and lower threaded buttons and stab wounds and defects on the end face.
C) Check the wear of the main shaft lining and replace it according to the situation.
D) Replace all seals and support rings.
3. washpipe, gooseneck pipe and lifting ring
A) Replace the washpipe, packing (floppy disk root, hard disk root), O-ring and snap spring.
B) Flaw the gooseneck and the lifting ring and issue a flaw detection report.
4. Drilling machine motor
A) Replace the main motor bearing, seal, gasket and grease nipple.
B) Measure the insulation of the coil of the main motor.
C) Assemble the main motor assembly according to NOV standard and maintain the motor bearings.
3.2. Rotary head assembly
1. Check the oil passage of the inner liner of the rotary head, ultrasonic or magnetic particle inspection shell, and issue a quality report.
2. Clean the oil passage and replace all seals and O-rings of the rotary head.
3. Assemble the rotating head, and conduct pressure test on the sealing of the rotating head according to NOV standard.
3.3.PH55 Pipe Handlerr assembly
1. Check the connecting pin between the pipe processor and the rotary head.
2. Replace the back tong hydraulic cylinder seal and the clamp spring.
3. Replace the seal of IBOP hydraulic cylinder.
4. Check the IBOP actuating structure and replace the sliding roller.
5. Assemble the PH55 pipe processor and back clamp hydraulic cylinder for pressure test.
3.4.IBOP assembly
1. Dismantle the upper and lower IBOP (pay special attention to the loosening when the platform throws the top drive)
2. Check the wear, corrosion and working conditions of the upper and lower IBOP, and carry out maintenance treatment according to the situation.
3. Replace the IBOP seal or replace the IBOP assembly.
4. Conduct pressure test, operate IBOP valve, and there is no leakage.
3.5. Motor cooling system
1. Replace the motor seal, bearing, grease nipple and gasket.
2. Check the insulation degree of fan motor coil.
3. Reassemble the fan cooling system and maintain the motor bearings.
3.6. Overhaul the brake system assembly.
1. Replace the brake disc and brake pad.
2. Check the seal of the brake fluid cylinder, steel pipe line or replace the brake fluid cylinder.
3. Check whether the encoder works well or replace it.
4. Reassemble the brake assembly.
3.7. Repair the transport skid and Carriage.
1. Carry out flaw detection on the transport skid and guide rail and issue a flaw detection report.
2. Check the guide rail connecting pin and replace it in time according to the working condition.
3. Check or replace the friction plate.
4. Replace the necessary accessories and lock the safety rope.
3.8 Hydraulic system
1. Check the steel pipe line for extrusion and damage, and replace all soft rubber pipelines.
2. Check the working condition of hydraulic pump, repair or replace it.
3. Check the hydraulic valve plate assembly and clean and repair the oil passage.
4. Check the solenoid valve and replace the damaged solenoid valve.
5. Replace the hydraulic oil filter assembly.
6. Replace all pressure test joints.
7. Check all pressure regulating valves and adjust or replace them according to technical standards.
8. Replace all accumulator seals and hydraulic cylinder seals.
9. Pressure test hydraulic cylinder and accumulator.
10. Clean the oil tank and replace the seal and gasket.
3.9 Lubrication system
1. Check the lubrication hydraulic motor and replace the damaged parts.
2. Replace the gear oil filter assembly.
3. Replace the seal and gasket.
4. Replace the gear pump.
3.10 Electrical system
1. Replace all pressure switches and encoders.
2. Replace solenoid valve and solenoid valve control line.
3. Replace the terminal block and seal of the junction box.
4. Check the cables and communication cables of each part of the top drive, and do explosion-proof treatment.
4. Assembly
1. Clean all parts.
2. Assemble each component assembly according to the assembly process standard.
3. Assemble the top drive assembly.
4. No-load test run, and issue a test report.
5. Cleaning and painting.
5. VDC maintenance
1. replace all buttons, alarm indicators, first rotation, tachometer and torque meter of VDC control panel.
2. Check the power board, I/O module and alarm horn of VDC.
3. Check the VDC cable plug.
4. Inspect the appearance of VDC and replace the sealing ring.
6. Maintenance of frequency conversion room
1. Check each circuit board of rectifier unit and inverter unit, and decide whether to replace accessories according to the feedback information and test results.
2. Test the modules of PLC control system, and decide whether to replace the accessories according to the feedback information and test results.
3. Test the brake unit, and decide whether to replace the accessories according to the feedback information and test results on the spot.
4. Replace the insurance, AC contact protector and relay.
7. Maintenance service items and time limit.
1. The quality guarantee period of top drive after maintenance is half a year.
2. Within half a year after the operation of the top drive, all the parts replaced during maintenance shall be replaced free of charge.
3. Provide free consulting services and technical guidance.
4. Train operators according to users' needs.
5. The warranty period of the following vulnerable parts is 3 months.
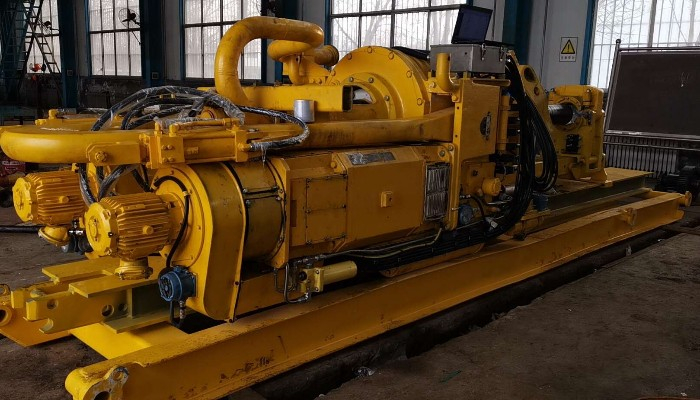